4-way black pipe fittings, like other pipe fittings, play a role in accommodating changes in elevation within a piping system. Here’s how they can be utilized for this purpose:
- Vertical Alignment:
- 4-way black pipe fittings can be used to create vertical sections in a piping system, allowing pipes to move up or down as needed to accommodate changes in elevation.
- Connection Points:
- These fittings provide connection points where pipes can be joined in a vertical or angled configuration. By using multiple fittings, the system can navigate changes in elevation smoothly.
- Branching and Diverting:
- 4-way fittings allow for branching and diverting pipes in different directions. This flexibility is useful when the elevation of the piping needs to change, and different routes are required.
- Elbows and Tees:
- Within the 4-way fitting, the presence of elbows and tees enables the creation of angles and turns in the piping system. Elbows facilitate changes in the horizontal plane, while tees allow for branching in the vertical and horizontal directions.
- Adjustable Angles:
- Depending on the design, some 4-way black pipe fittings may allow for adjustable angles. This feature permits the fine-tuning of the angle of the pipes, providing adaptability to changes in elevation.
- Support Structures:
- The fittings contribute to the overall support and stability of the piping system. 4 way black pipe fitting This is particularly important when dealing with changes in elevation, as proper support helps prevent sagging or stress on the pipes.
- Use of Couplings:
- Couplings, combined with 4-way fittings, can be employed to connect pipes seamlessly, allowing for elevation changes without compromising the structural integrity of the system.
- Expansion Joints:
- In situations where the piping system may experience thermal expansion or contraction, expansion joints can be incorporated with 4-way fittings to absorb movement and accommodate changes in elevation.
- Flexible Piping Sections:
- Utilizing flexible pipe sections in conjunction with 4-way black pipe fittings allows for some degree of movement and adjustment, making it easier to navigate changes in elevation.
- Proper Sloping:
- When accommodating changes in elevation, it’s essential to maintain proper sloping in the pipes, especially in drainage systems. 4-way fittings can be positioned to ensure the desired slope for efficient flow.
- Anti-Siphon Features:
- In applications where avoiding backflow is critical, 4-way fittings with anti-siphon features can be employed to prevent water from flowing in the wrong direction due to changes in elevation.
- Sealing and Leak Prevention:
- Ensuring proper sealing at joints is crucial when dealing with changes in elevation. The 4-way fittings, along with gaskets or sealing materials, contribute to leak prevention and system integrity.
When using 4-way black pipe fittings to accommodate changes in elevation, it’s important to adhere to industry standards, follow manufacturer guidelines, and consider factors such as system pressure, material compatibility, and the specific requirements of the application. Proper planning and installation contribute to the overall efficiency and longevity of the piping system.
What types of testing are typically conducted on 4-way black pipe fittings to ensure quality and reliability?
Various testing procedures are typically conducted on 4-way black pipe fittings to ensure their quality, reliability, and compliance with industry standards. These tests are essential to verify that the fittings can withstand operational conditions, pressures, and potential stresses they may encounter in various applications.
Common types of testing for 4-way black pipe fittings include:
- Visual Inspection:
- A visual inspection is the initial step to identify any visible defects, irregularities, or surface imperfections in the 4-way black pipe fittings. This includes checking for proper finishing, absence of cracks, and overall conformance to specifications.
- Dimensional Inspection:
- Measurements and dimensional checks are performed to ensure that the 4-way black pipe fittings meet the specified dimensions and tolerances. This includes assessing the accuracy of angles, diameters, and thread dimensions.
- Material Composition Analysis:
- Material composition analysis verifies that the materials used in the construction of 4-way black pipe fittings conform to specified standards. This ensures the proper alloy or composition required for strength, corrosion resistance, and other relevant properties.
- Hydrostatic Testing:
- Hydrostatic testing involves pressurizing the 4-way black pipe fittings with water or another suitable fluid to a specified pressure level. This test checks for leaks, assesses the structural integrity under pressure, 4 way metal pipe connector and ensures that the fittings can withstand the intended operational loads.
- Tensile Testing:
- Tensile testing assesses the strength and ductility of the material by subjecting the 4-way black pipe fittings to axial pulling forces. This helps determine the tensile strength, yield strength, and elongation properties of the material.
- Impact Testing:
- Impact testing evaluates the resistance of 4-way black pipe fittings to sudden impacts. This is particularly important in applications where the fittings may be exposed to mechanical shocks or dynamic loading conditions.
- Bend Testing:
- Bend testing assesses the ductility and integrity of the fittings by subjecting them to bending forces. It ensures that the fittings can withstand bending without cracking or failing.
- Flattening Testing:
- Flattening tests involve flattening a section of the 4-way black pipe fittings to check their deformation behavior. This is crucial for applications where the fittings may experience external pressure or compression.
- Thread Inspection:
- Thread inspection ensures that the threads on the 4-way black pipe fittings meet the specified standards. It involves checking thread dimensions, pitch, and taper to ensure compatibility with mating components.
- Corrosion Resistance Testing:
- Corrosion resistance testing evaluates the ability of the 4-way black pipe fittings to resist corrosion in different environmental conditions. This is essential, especially in applications where the fittings may be exposed to corrosive substances.
- Non-Destructive Testing (NDT):
- NDT techniques such as ultrasonic testing, magnetic particle testing, or dye penetrant testing are used to detect internal defects, cracks, or irregularities without causing damage to the fittings.
- Fatigue Testing:
- Fatigue testing involves subjecting the 4-way black pipe fittings to repeated cyclic loading to assess their fatigue resistance. This is particularly relevant in applications where fittings may experience repetitive stress.
- Sealing Performance Testing:
- Sealing performance testing involves assessing the ability of threaded or sealed connections in the 4-way black pipe fittings to prevent leaks under pressure. It ensures the reliability of the fittings in fluid-carrying systems.
- Fire Resistance Testing (if applicable):
- In certain applications, especially those involving fire safety, 4-way black pipe fittings may undergo fire resistance testing to ensure their performance under elevated temperatures.
Manufacturers may conduct a combination of these tests based on industry standards, customer requirements, and the intended application of the 4-way black pipe fittings. Adhering to these testing procedures helps ensure the quality, reliability, and safety of the fittings in various operational conditions.
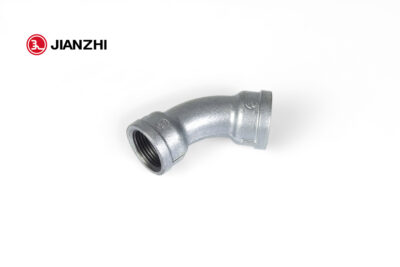